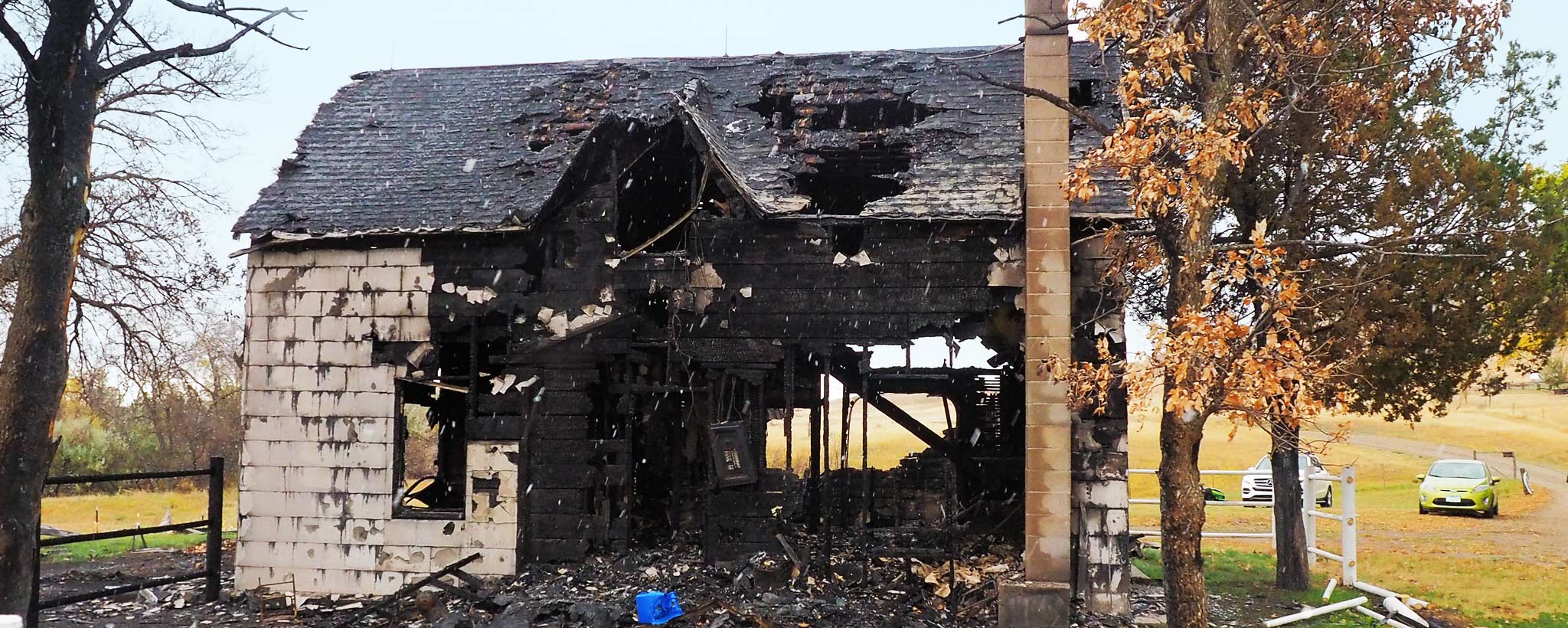
Mother Nature — A Powerful and Destructive Beast
Let’s face it, Mother Nature is a force to be reckoned with – flooding, hurricanes, earthquakes, tornados, straight-line wind, hail, forest fires, lighting, and snowstorms. There is no off-season for Mother Nature or in the insurance world. In addition, the cost of catastrophic weather events is staggering. Hurricane Katrina, the most expensive weather event in the United States history, reportedly caused $50 billion in insured losses.
In recent years, Colorado has seen multiple costly weather events.
2017 May hail storm
2013 September historical flooding
2013 Summer wildfires
2012 Summer wildfires
Just this past 2020 produced claims which resulted in hundreds of millions of dollars in damages. In the cases of the May 8, 2017, hail event and the September 2013 flood, there were over $2 billion in reported damages.
Colorado Wildfire Insurance Costs
Wildfire insurance costs hinge on a number of factors, including the number of primary homes in the area (as compared to vacation homes and cabins), their estimated value and the amount of insurance coverage on the properties.
Year | Fire | Insured Loss ($ Millions) |
2020 Dollars ($ Millions)* |
2012 | Waldo Canyon, Colorado Springs | $453.7 | $509 |
2013 | Black Forest, near Colorado Springs | $420.5 | $465 |
2012 | High Park, near Fort Collins | $113.7 | $127.6 |
2010 | Fourmile Canyon, northwest of Boulder | $217.0 | $256.5 |
2002 | Hayman, southwest of Denver | $38.7 | $55.4 |
2002 | Missionary Ridge, near Durango | $17.7 | $25.3 |
2002 | Coal Seam, Glenwood Springs | $6.4 | $9.17 |
2002 | Iron Mountain, near Cañon City | $7.5 | $10.74 |
*2019 estimated cost calculations based on the Consumer Price Index.
Colorado’s Most Costly Hail Storms
With the exception of the May 22, 2008, Windsor tornado and the hail storm that hit Pueblo on July 29, 2009, Colorado’s ten most costly hail storms were centered in the Denver Metro area (which makes sense, because that’s where the largest concentration of property in the state is located).
DATE | LOCATION | COST (MILLIONS) | 2020 COST (MILLIONS) |
May 8, 2017 | Denver Metro | $2.3 Billion | 2.4 Billion |
July 20, 2009 | Denver Metro | $767.6 | $923.5 |
July 11, 1990 | Denver Metro | $625.0 | $1.23 Billion |
June 6-15, 2009 | Denver Metro | $353.3 | $425 |
July 28, 2016 | Colorado Springs | $352.8 | $379.4 |
June 6-7, 2012 | CO Front Range | $321.1 | $360.9 |
June 13-14, 1984 | Denver Metro | $276.7 | $687.3 |
June 18-19, 2018 | North Denver and Denver Metro | $276.4 | $284 |
July 29, 2009 | Pueblo | $232.8 | $280 |
October 1, 1994 | Denver Metro | $225.0 | $391.8 |
September 29, 2014 | Denver Metro | $213.3 | $232.5 |
May 22, 2008 | Windsor | $193.5 | $231.9 |
*2020 estimated cost calculations based on the Consumer Price Index.
Steps to Determine Severity of Damage
While Golden Forensics has not yet figured out a way to control Mother Nature, we can provide a clear scope of damages, repair and restoration recommendations, and cost of repair estimates.
The first area we will look at is fire-related damage. This past year, we saw record-setting forest fires in Colorado. It was common to wake up in the Denver metro area to an orange hue in the sky, the smell of fire, and ash on your car. While the forest fires caused destruction to many homes and businesses in Colorado, fires are caused every day by faulty electrical components or wiring, mechanical equipment, candles, cigarette butts, and even the spontaneous combustion of oily rags.
1. Determine Post-fire Integrity
The biggest question after a fire is simply can the structure be repaired, or does it have to be torn down and rebuilt? This decision can be influenced by a number of variables; however, the structural engineer can provide insight into the building code requirements and the condition of the remaining structural components, and if these components can be salvaged. Evaluating these components can be challenging because wood, steel, and concrete are all affected differently by fire. However, each component has specific basic indicators to look for when determining its post-fire structural integrity.
The biggest question after a fire is simply can the structure be repaired, or does it have to be torn down and rebuilt?
While not directly related to a fire, the authority having jurisdiction (AHJ) (local building official) is very much a part of the rebuilding process. An important initial step in the rebuilding process is to first understand the AHJ’s building code and what it means for the reconstruction process. Most jurisdictions in Colorado have adopted an edition of the International Code Council (ICC) as the basis for their own code and then amended it as they deem necessary. The ICC is broken down into a number of references, the most common being the International Building Code (IBC), which primarily deals with commercial structures. The International Residential Code (IRC) pertains to one and two-family dwellings and the International Existing Building Code (IEBC) addresses the different categories of work that can be completed on existing buildings including repairs, alterations, change of occupancies, and additions to name a few. Typically, when dealing with repairing fire damage, the work can be categorized as a “repair.”
[A] REPAIR the reconstruction or renewal of any part of an existing building for the purpose of its maintenance or to correct repair.
Definition of repair as defined by the 2015 IECB Section 202.
2. Check Building Codes Regarding Substantial Structural Damages
In general, the building code will allow an existing structure to be repaired to its original condition if there is less than “substantial structural damages” as defined by the code. If the damages are considered “substantial structural damage,” more formal calculations may be needed to ensure the existing building as a whole is in compliance with the current building code.
You may be asking yourself at this point, “how do you know if the structure has sustained ‘substantial structural damage?’” and that is a good question. The definition from the code is provided below. If you find yourself at this point, it may be best to just give us a call.
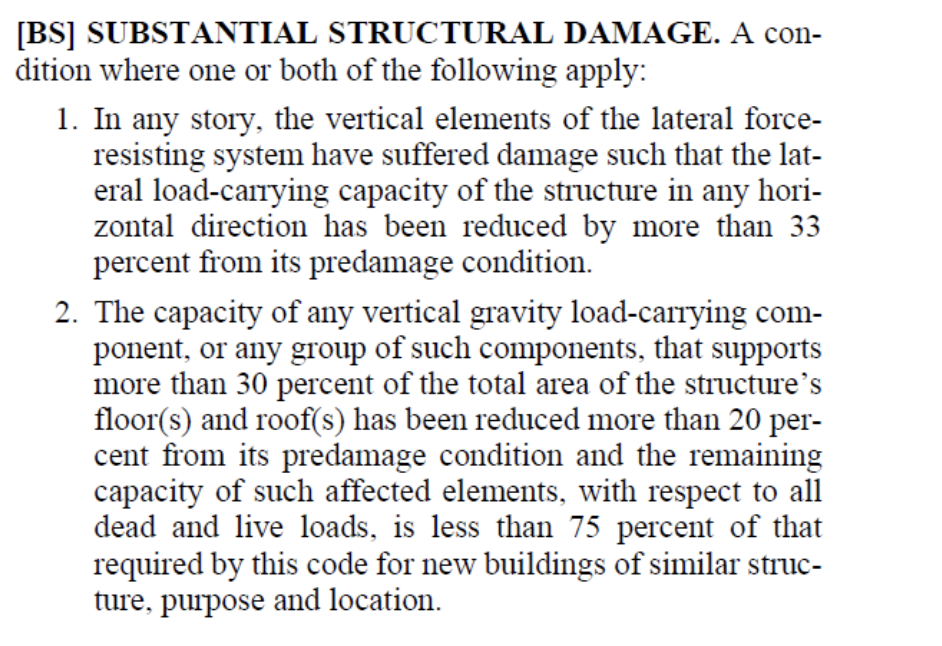
Definition of substantial structural damage per 2015 IEBC Section 202.
3. Evaluate if Dangerous Conditions Can Be Eliminated
For buildings that have not been damaged beyond the “substantial structural damage” threshold, they can be returned to their original condition; however, regardless of the extent of the repair, the code (Section 606) requires that dangerous conditions be eliminated, and any new structural members, components or connections follow the currently adopted building code. Finally, this all of course comes with the caveat that the building official can still make changes if deemed to be a life-safety issue.
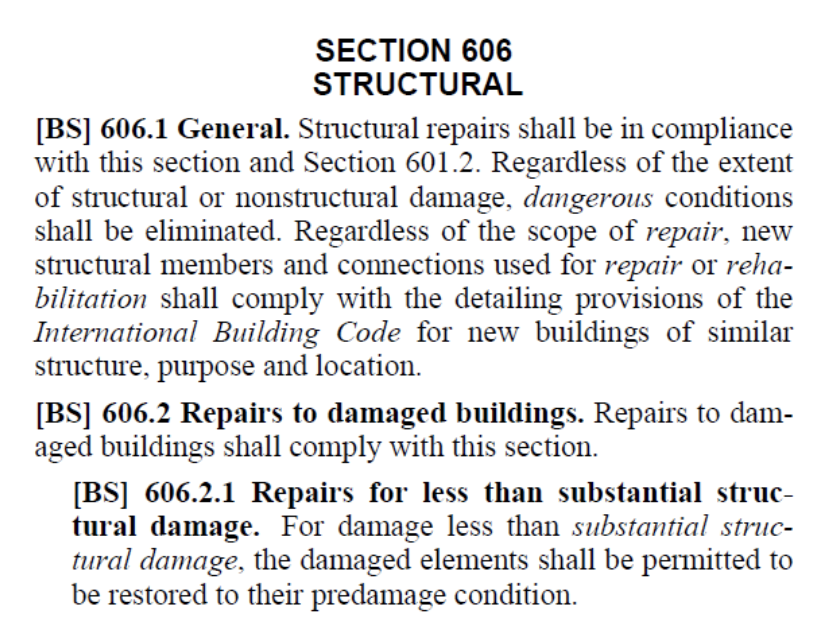
2015 IEBC Section 606.2.1, Repairs for less than substantial structural damage.
Common Building Materials and Fire Exposure
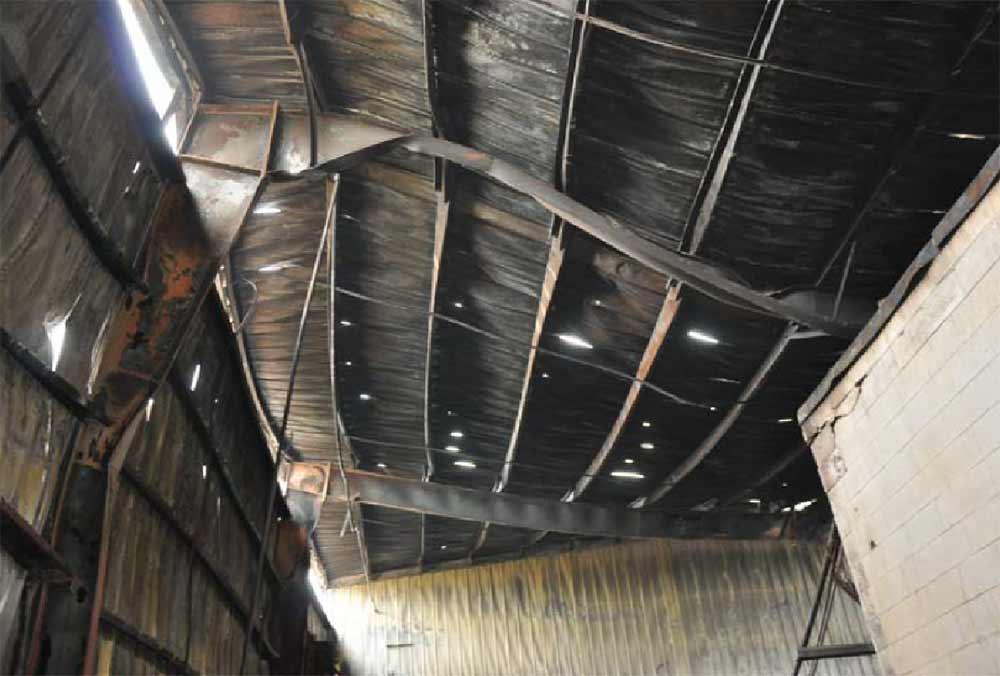
Wood
The most common building material in residential structures and sometimes used in commercial structures, is, as you could guess, wood. Wood is an extremely good building material for smaller structures with overall lighter loads, it is easy to work with, relatively inexpensive, and has remarkably good structural properties, especially engineered lumber. Unfortunately, wood is the most combustible building material. Wood can ignite at around 450°F, with char layers developing around 550°F. Overall, these are relatively low temperatures considering the extreme temperatures that can be produced by a typical house fire. The good news for wood members is once the wood member has developed a char layer, the char layer acts as an insulator and protects the inner layers of the wood requiring greater temperatures to degrade the inner core.
The Char Layer
The char layer obviously has no structural capacity; however, the degraded layers can be removed through scraping or media blasting, and the remaining wood still contains residual structural capacity, although less than its original capacity prior to the fire. A structural engineer can take the remaining wood section and determine if the member contains sufficient remaining strength to be used in service again.
These types of calculations are best used for framing members having a larger initial cross-sectional area and are not recommended for smaller, light-framing members such as 2X’s. 2X members that have sustained significant charring should be removed completely. Typically, these members are designed up to their load capacity and do not contain enough residual strength to handle a reduction in cross-sectional area and overall reduction in strength. However, a char layer of 1/16-inch or up 10% of the cross-section area could be justified depending on the loading on the member.
Wood Trusses
Wood trusses should be treated the same way as 2X members; however, one additional condition needs to be addressed. The connection of the truss member is usually made with a steel gusset plate. If there is damage or discoloration of the plate or the wood members being connected under the plate are charred, the connection is considered to have failed and it is recommended that the members and plate be repaired or replaced.
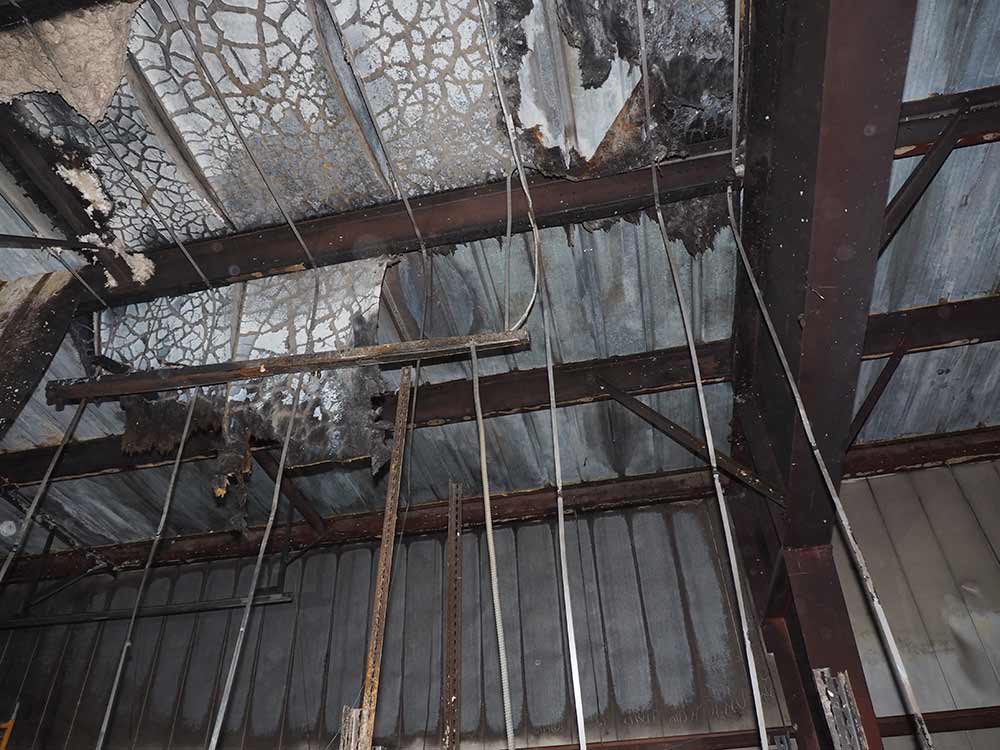
Steel
Steel is a bit less straightforward to analyze after a fire than wood. If steel is exposed to elevated temperatures for an extended period of time, metallurgical changes can start occurring. However, if the steel member has not been exposed to temperatures in excess of 1,200°F for an extended period of time, it is unlikely these metallurgical changes have occurred, and the steel member will retain nearly 100% of its pre-fire strength.
The condition of the materials around the steel element can be a good indicator of the heat the steel member may have experienced. The National Fire Protection Association (NFPA) Guide for Fire and Explosion Investigations (921) provides a table for the typical melting temperature of common materials found in a building.
For example, if plastics are still in place or wood floor joists are still framed into a steel beam, it is likely the steel beam did not sustain damaging heat as the temperature required to damage the steel beam is significantly higher than the melting temperature of plastics (190°F – 257°F for ABS) or the ignition temperature of wood (450°F). Conversely, if aluminum or copper metals are found to be melted near the steel member then further evaluation may be required to determine if the member has been damaged by the fire.
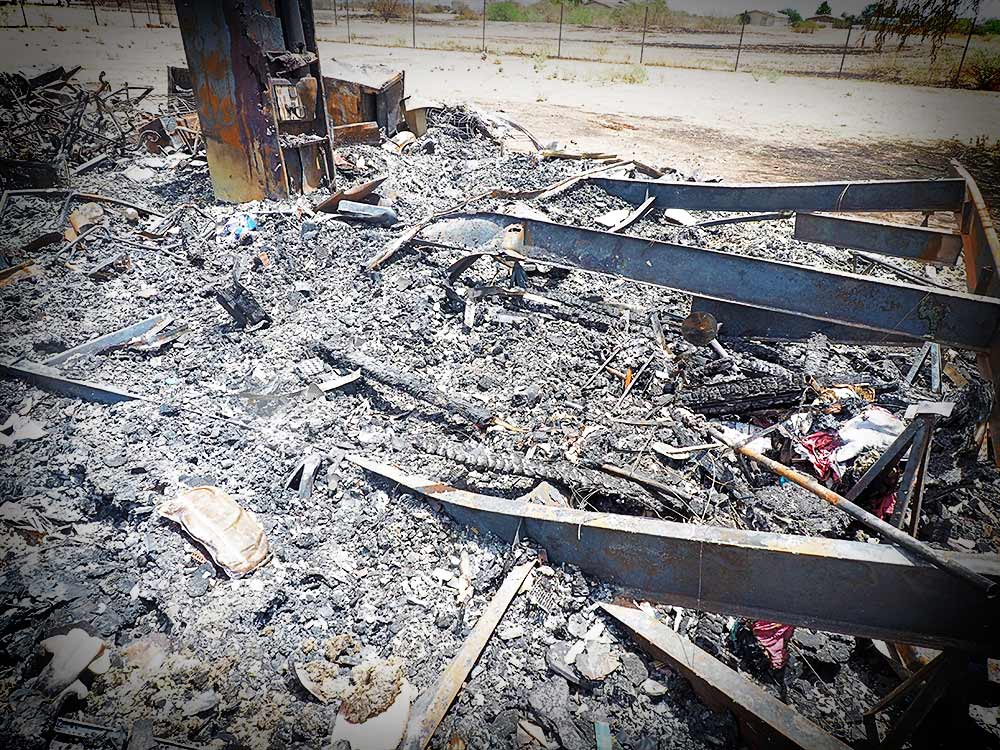
Testing Steel for Structural Integrity
Surface Hardness Test
Specialized tests can be performed to determine if the properties of a steel member have been affected by the fire. A non-destructive test such as the surface hardness test can provide insight if the steel member has been exposed to elevated temperatures by measuring the approximate tensile strength. Destructive testing can also be completed by removing a steel coupon which can be tested to see if the properties of the steel have been adversely affected by the fire.
Evaluate Straightness, Plumbness, and Heat Exposure
The good news is that steel is typically unaffected by smaller fires (with less heat). A few simple measurements and observations can be made to gain insight into the condition of the steel member. A steel beam, for example, can be evaluated for straightness or plumbness and dimensional measurements can be verified to ensure the beam was not exposed to elevated temperatures. Even if a steel member has been affected by a fire in the form of a deformation, it is still possible to repair the member. Members may be heat straightened to remove slight deformations, or even reinforced with steel plates, channels, or angles. However, if a member has been severely deformed, unless under extreme conditions, (the removal of the member would create an unsafe condition) it is typically more economical to replace the steel member.
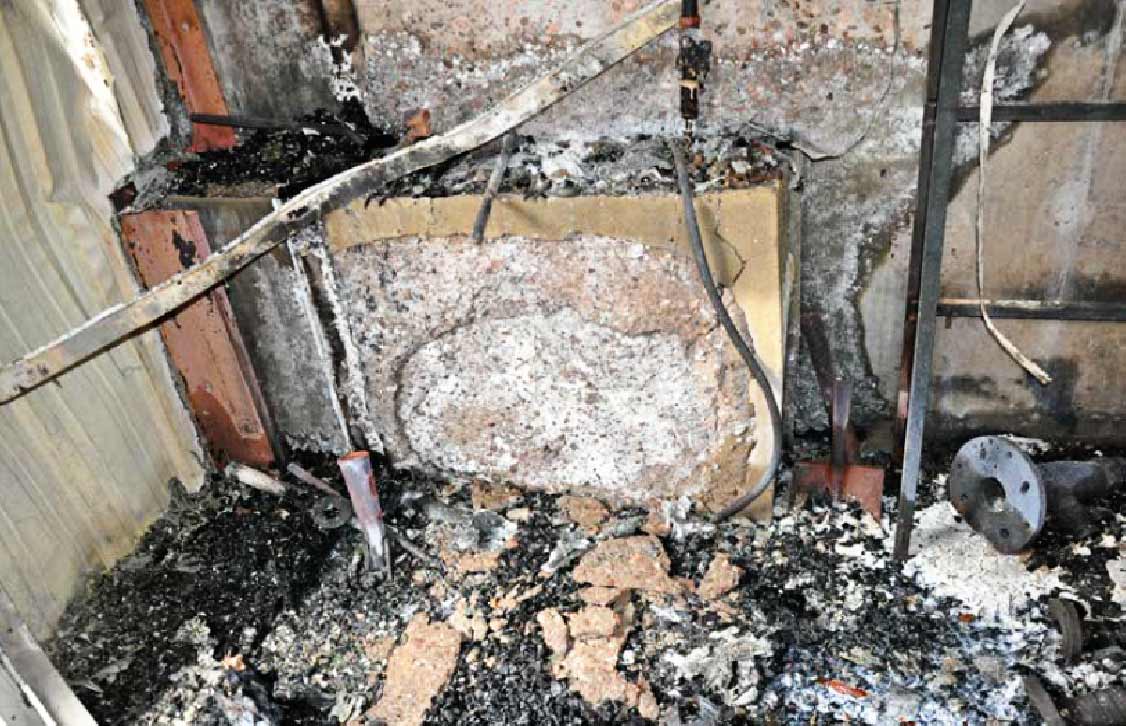
Concrete
Concrete, like steel, is not straightforward, but there are simple observations and non-destructive testing techniques that can be performed to help assess the concrete. Nondestructive evaluation of cast concrete consists of three types of observations: visual observation, sounding, and rebound hammer testing.
Physical and Visual Evaluation
First, areas of the concrete that have been exposed to a fire are visually evaluated for evidence of distress resulting from the fire. Physically observable changes or distress from heat exposure include cracks, delamination, spalls, and/or color changes.
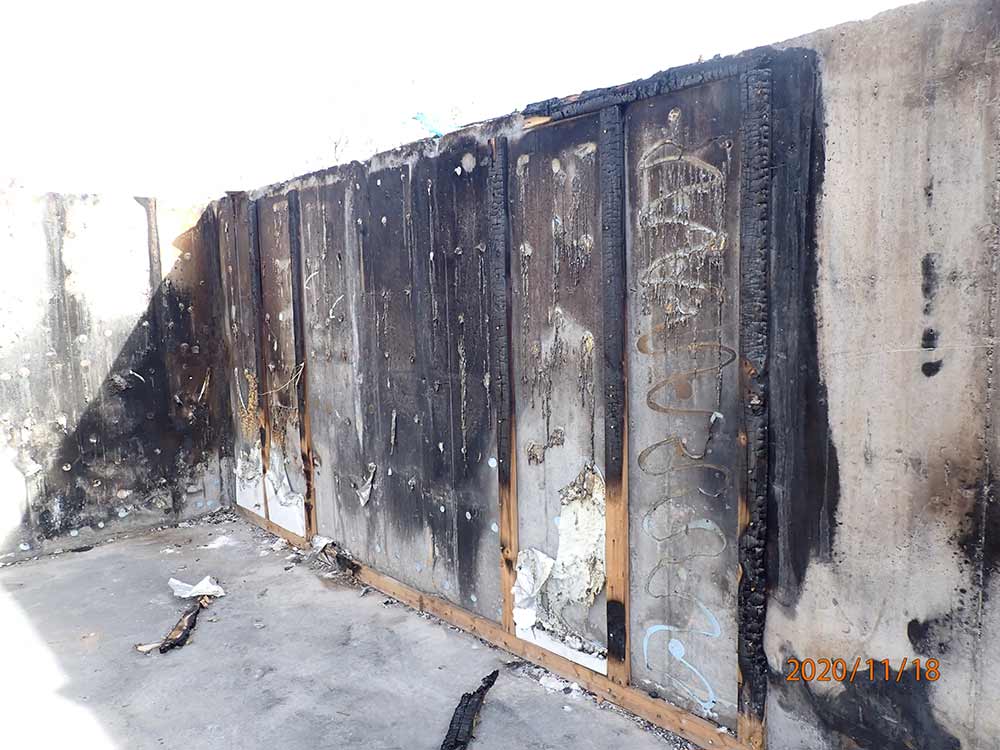
1. Color
Color changes in the concrete can help indicate if the strength of the concrete has been compromised. Color changes to a red or pink hue or buff-color may indicate heat damage.
Soot
It should be noted that wall sections that are soot-covered (black) typically have not been exposed to high heat. Soot is where the smoke from the fire has settled onto a surface. Typically, soot will accumulate only on surfaces that are cooler than the fire. It is also important to observe areas of the framing that have remained on or around the concrete. Because concrete can resist high temperatures before degradation, most combustible materials will be consumed prior to damage occurring to concrete sections.
2. Audible Evaluation
Second, areas of the concrete that have been exposed to the fire can be audibly sounded using a hammer to check for delamination of the concrete. In general, when struck by a hammer, if the concrete makes a “ping,” it is considered to be solid and structurally intact. On the other hand, if the concrete makes a “thud,” this can indicate the concrete has delaminated and has potentially been adversely affected by the fire. A chain drag can additionally be used on the cast concrete slabs. Similar to sounding a wall with a hammer, a chain-drag can audibly identify locations of delamination which may have been caused by the fire.
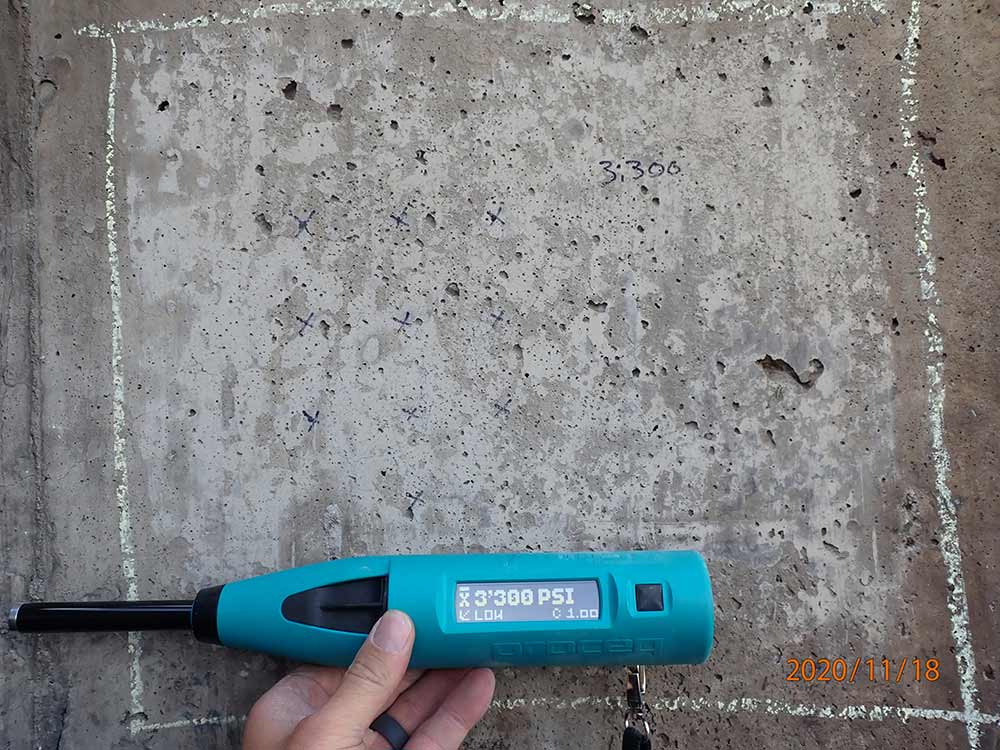
3. Measure the Strength
Third, areas of concrete that have been exposed to the fire can be evaluated for their remaining compressive strength using a Schmidt® rebound hammer. Testing can be completed by measuring the compressive strength of the concrete in sections where it was unaffected by the fire, then comparing it to compressive strength of the concrete in sections which through observation (visual and sounding) indicate it has been exposed to fire. These results can be compared to determine if there was an appreciable reduction in the compressive strength of the concrete between the wall sections.
4. Secondary Comprehensive Tests
Of course, there are more extensive nondestructive and destructive tests that can be completed to provide more definitive results, such as ultrasonic pulse velocity testing or core sampling. While these are more comprehensive tests and their implementation may be required, they would usually not be the first step taken when evaluating concrete for damages as a result of a fire.
Smoke Damage
Smoke from a fire which has permeated the entire structure and water damage from the copious amounts of water used to extinguish the fire can result in as much damage as the actual fire itself in some instances. There are a number of techniques used to mitigate the smoke including media blasting, chemical washes, thermo-fogging, ozone, and sealers. Likewise, wood framing typically will retain its original strength if promptly dried out after a firefighting activity. The prompt drying of the structure is needed to prevent the decay of the wood member and microbial growth. The Institute of Inspection Cleaning and Restoration Certification (IICRC) provides industry-accepted standards to properly address these issues. Golden Forensics has building consultants with IICRC Certification that can assist in the restoration of your structure.
Golden Forensics provides the necessary services to evaluate a fire-damaged structure that saves you money and time. Golden Forensics provides scientific answers to complex forensic engineering problems.
References
- Rocky Mountain Insurance Information Association (RMIIA), http://www.rmiia.org/index.asp
- 2015 Edition of the International Existing Building Code, Published by the International Code Council.
- Gosain, Narendra; Drexler, Ray; Choudhuri, Dilip; Evaluation and Repair of Fire Damaged Buildings. Structural Engineering Magazine, September, 2008.
- National Fire Protection Association (NFPA) 921; Guide for Fire and Explosion Investigations, 2017 Edition, Table 6.2.8.2.
- Ross, Robert; Brian K.; Wang, Xiping; White, Robert; Pellerin, Roy; Post-Fire assessment of structural wood members. Wood and timber assessment manual . Madison, WI: Forest Products Society: 29-46 Chapter 4.
- Tide, R.H.R.; Integrity of structural steel after exposure to fire. Engineering Journal, First Quarter 1998.
- Kakade, Ashok; Condition Evaluation of Fire-Exposed Concrete Foundation, Concrete Science, January 2019.
- Condition Evaluation of Fire Exposed Concrete Foundation, Concrete Science® Inc.